Injection molding is a common manufacturing process used to produce plastic parts. It involves injecting molten plastic material into a mold cavity and allowing it to cool and solidify into the desired shape.
One key component of the injection molding process is the die or mold. This is the custom-machined metal tool that forms the mold cavity and gives plastic parts their shape. To produce quality parts efficiently, the injection molding die needs to be cooled effectively during the molding cycle. This is why injection molding dies are typically water cooled. As a professional plastic injection molding manufacturer, I will talk about water cooling in injection molding.
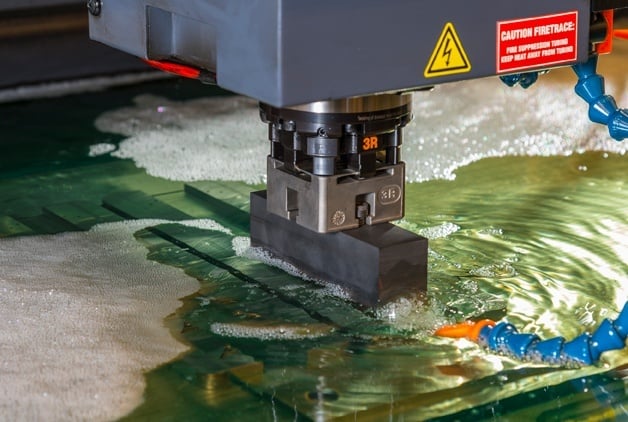
Why is cooling important in injection molding?
Cooling is a critical phase of the injection molding process for several reasons:
- It allows the molten plastic to solidify fully and stabilize in the proper dimensions of the die. Insufficient cooling can lead to defects like warpage and shrinkage.
- It impacts cycle times and productivity. The cooling process can take up significant time in the molding cycle, so efficient cooling translates to faster cycle times and higher part output.
- It affects the longevity of the mold. Effective cooling helps minimize thermal stresses on the injection molding die overtime.
Essentially, cooling is pivotal for producing dimensionally accurate parts with the desired mechanical properties, surface finish and at optimal cycle efficiencies. This explains why cooling channels and cooling media are integral aspects of injection mold design.
Why are injection molding dies typically water cooled?
There are several reasons why water reigns as the cooling agent of choice in most injection molding applications:
Cost-effectiveness
Water offers excellent heat transfer capabilities at a fraction of the cost of oil or other fluids, making it extremely cost-effective. The abundant availability of water also contributes to lower operational costs for molders.
Heat transfer properties
With a high specific heat capacity and thermal conductivity, water can absorb and transfer substantial amounts of heat rapidly. This helps quickly cool molten plastic inside molds and enables shorter cycle times.
Lower carbon footprint
Unlike chillers using refrigerants, water cooling systems powered by cooling towers have a significantly lower carbon footprint. This makes water cooling a more environmentally sustainable option as well.
Versatility
The properties of water like temperature, flow rate and additives can be easily adjusted to meet the specific cooling demands of different plastic resins or mold designs. This versatility also enables water to be used across various equipment like chillers, pumps and heat exchangers.
Ease of use
Being readily available, water cooling systems are also simpler to set up, maintain and operate compared to oil. And unlike oil, water is safer for workers handling the injection molding equipment.
So in a nutshell, water emerges as the preferred cooling medium in injection mold dies because it’s cost-effective, transfers heat rapidly, has a lower carbon footprint, is versatile and easy to use. These inherent advantages have cemented water’s status as the cooling agent of choice in plastic injection molding applications.
How does water cooling work in injection molds?
Integrating water cooling into injection molds involves strategically designing cooling channels called bubblers, baffles or thermal pins into the mold. Chilled water, typically maintained between 50-90°F, is then pumped through these channels to draw heat away from the molded plastic part.
As the hot molten plastic enters the die cavity, the cooling water absorbing the transferred thermal energy while ensuring the plastic solidifies uniformly. This cooled water then flows back to a chiller unit where the absorbed heat gets transferred to the environment via cooling towers. The water is recooled to the optimal temperature before starting the cycle again.
Proper water cooling channel placement and design are pivotal to facilitate uniform cooling. Uneven cooling can give rise to defects like sinks, voids or warpage. Factors like the plastic resin used, part wall thickness and flow channel dimensions influence cooling channel configurations.
Additionally, flow turbulence manipulation using baffles or tightly controlled temperatures and flow rates play key roles in optimizing heat transfer. All of this put together enables water cooling to rapidly cool injection molded parts in 25-40 seconds while maintaining dimensional accuracies.
Conclusion
Effective cooling forms the backbone of efficient injection molding operations. And water cooling leverages rapid heat removal at cost-effective rates to deliver on these process cooling needs.
Strategic cooling line design paired with precision temperature and flow control unlocks water’s versatility in catering to different molding applications. By allowing rapid, uniform plastic solidification within dies, water cooling paves the path for faster cycles, higher throughput and impeccable part quality.
So next time you use a plastic product, remember water cooling’s silent role in its high-quality, precision manufacturing!