Plastic injection molds can cost tens of thousands of dollars or even hundreds of thousands of dollars depending on the size, complexity, materials, and other factors. As we’ll explore here, creating these precision-engineered tools is an extremely complex process that requires significant investments in design, materials, machinery, labor, maintenance, and more. As a professional plastic injection molding manufacturer, I will list them in detail in this article.
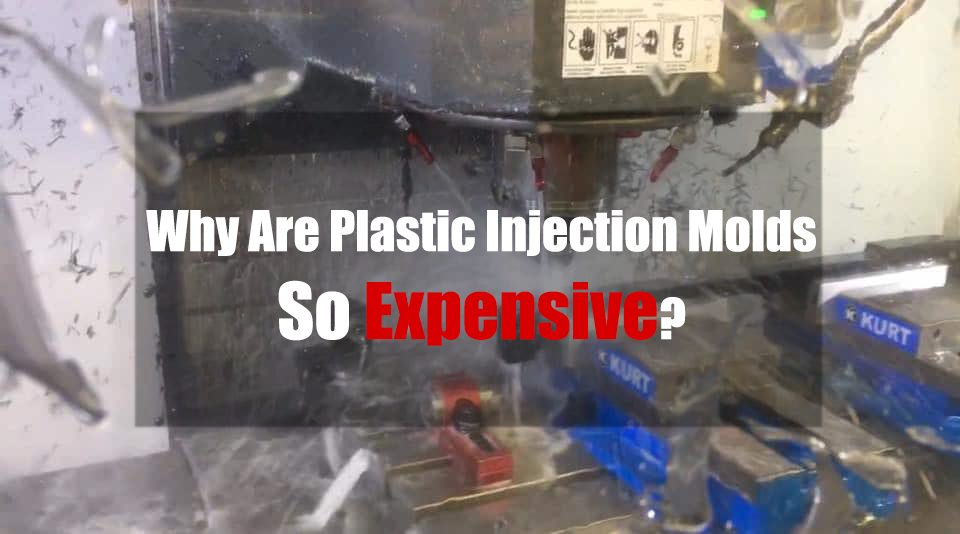
Why Are Plastic Injection Molds So Expensive?
High Raw Material Costs
The raw materials for injection molds are a significant cost driver. In most cases, molds are made from premium grades of steel or aluminum alloys. These metals are much more expensive than standard structural steels due to enhanced properties like:
- Hardness – The mold cavity needs to resist dents, scratches, and wear even after cycles numbering in the millions. Harder metals better retain their molding accuracy.
- Toughness – The metals need enough ductility so the mold can withstand high pressure injection cycles without cracking or outright failure.
- Thermal properties – Steels and alloys are chosen that can cope with molten plastic injection while also rapidly shedding heat during the cooling cycle.
On average, the mold steel itself accounts for around 25-35% of the total mold cost depending on the size and complexity. And that’s before a single cavity has been machined!
Intricate, Custom Machining
Once the stock steel blocks have been prepared, the complex machining process begins using computer-controlled equipment.
Features like the mold cavity, runners, gates, ejector pins, and cooling lines need to be precision machined to within 0.005 inches (for scale, a human hair is around 0.003 inches wide). For critical dimensions, specialized wire EDM machining is used.
As you might imagine, for large molds with many cavities and complex part geometries, the programming time alone can amount to hundreds of hours. This specialized mold machining accounts for around 40-50% of the total mold cost.
Supplementary Costs Quickly Add Up
Beyond the raw mold block and CNC machining, there are quite a few supplementary expenses that make up the remainder of the mold price tag:
Design and Engineering – Creating an optimal mold design from scratch requires experienced engineers using advanced software. This can cost $5,000+ for a complex project.
Heat Treating – To further enhance the mold’s hardness and resilience, secondary heat treatments are often applied. This adds several thousand dollars depending on mold size.
Hand Polishing – While CNC machining is incredibly precise, the final mold cavity is hand-polished by master mold makers to achieve a flawless mirror finish.
Certification – For regulated industries like medical and aerospace, molds require certified materials and extensive validation testing. This can cost tens of thousands.
Assembly – Dozens of components like ejector pins, cooling lines, and venting need to be assembled with precision alignment.
Shipping – Precision equipment plus insurance easily adds thousands for shipping and handling costs.
And this is just scratching the surface – other costs stem from project management, quality assurance equipment/personnel, shop consumables, energy usage, and margin for the mold maker.
Why Are Some Molds More Expensive?
As described above, there are baseline costs to produce even simple plastic injection molds. However, molds for complex components with tight tolerances or special features usually cost vastly more.
Tighter Tolerances – When molded parts need ultra-high precision, the mold has to achieve those same tight tolerances, often down to +/- 0.005 inches or below. This exponentially increases machining programming/run times.
Complex Geometries – Intricate part contours, hollow forms, or negative draft angles require complex toolpaths and side-action cams that have to be integrated into the mold tool. Huge added costs.
Exotic Alloys– To withstand aggressive filling with materials like glass or carbon fiber filled polymers, the mold has to be machined from far more expensive tool steels.
Side Actions – Lifters, sliders, unscrewing gear, and undercuts add moving components powered by hydraulic or mechanical side actions to assist in releasing completed molded parts.
Conformal Cooling – For ultra-fast cycle times, some molds are machined with conformal cooling channels. But programming these intricate passageways often requires another ~100 programming hours.
Multiple Cavities – Larger family molds with 4, 8, 16+ impressions substantially drive up costs. More impressions equal more machining operations.
Inserts – When molded parts need areas with different surface finishes or mechanical properties, custom fitted pieces are inserted into the mold cavity.
Long Term Cost Considerations
While the upfront cost to produce plastic injection molds is admittedly huge, each mold ultimately facilitates mass production injection molding runs numbering into the millions of low cost per-piece parts.
Over years of continual operation, even expensive high-end molds easily pay for themselves when tallying up how many plastic components they churn out.
And thanks to robust construction from premium materials, properly maintained injection molds often deliver reliable performance for well over 25 years before needing replacement.
Key Takeaways on Plastic Injection Mold Costs
In review, here’s a quick summary explaining why plastic injection molds demand serious capital investment:
- Raw mold blocks start from expensive tool steel and alloy grades to withstand years of production.
- Intricate custom machining and polishing is needed to achieve micron-level accuracy.
- Many supplementary expenses like design, testing, assembly, and shipping add up.
- Total costs ramp up exponentially for complex geometries, exotic polymers, and tight tolerances.
- However, per-piece cost at huge production volumes is very economical.
- Properly maintained molds operate reliably for decades, producing millions of parts.
I hope this gives you a better grasp of the immense precision, process complexity, and outright commitment required to produce plastic injection mold tooling! Let me know if you have any other questions.