Will 3d printing replace injection molding has been a hot debate recently. With advancements in 3d printing technology, some argue that it’s only a matter of time before additive manufacturing replaces conventional plastic injection molding.
In this post, I’ll analyze the capabilities of both processes to determine if 3d printing really can replace injection molding for good.
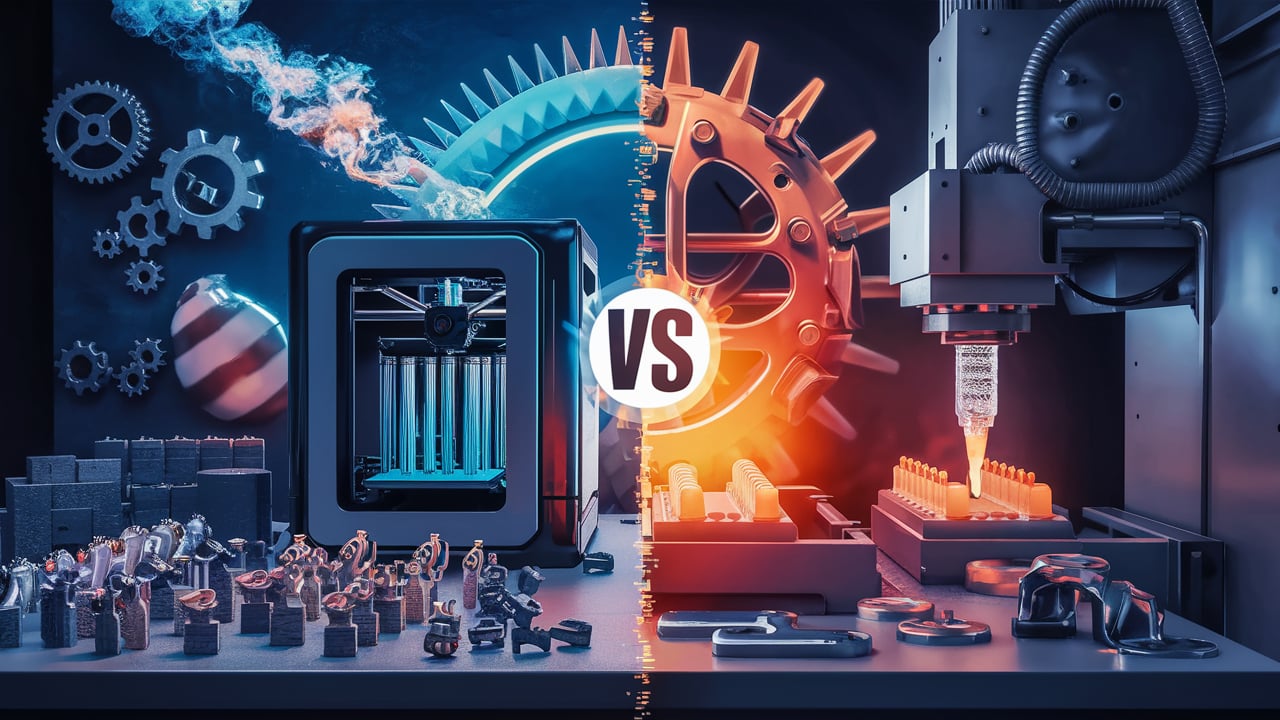
3D Printing and Injection Molding
As a regular plastic injection molding manufacturer, I don’t have extensive technical knowledge on 3D printing manufacturing processes.
So I reached out to John Smith, founder of ACME 3D Printing, for his take.
He told me: “3d printing has come a long way in recent years. But injection molding still holds some key advantages in terms of cost, quality, and production capacity.”
While 3d printing shines for rapid prototyping and custom parts, injection molding is king when you need 100,000+ identical plastic items.
However, there are indications that 3d printing could catch up soon:
- Scalability – Leading 3d printing companies like Carbon are developing production-scale systems capable of outputs to rival injection molding.
- Costs – The per-part cost of 3d printing is dropping. And when you factor in the overhead of injection molding systems, the crossover point gets nearer.
- Materials – New advanced 3d printing materials offer mechanical properties on a par with injection molding plastics.
- Design Complexity – 3d printing handles intricate geometries that injection molding simply can’t match.
So while injection molding maintains the edge for now, the advances in 3d printing technologies could position it as a replacement in the future.
Comparing Injection Molding Against 3d Printing
To get a balanced picture, let’s compare some of the key attributes between injection molding and 3d printing:
Scalability
Injection molding is king when it comes to scale. The whole process is optimized for volume production – you can easily create hundreds of thousands of identical components.
3d printing has traditionally been the realm of prototypes and low batches. But that is evolving…
Take HP’s Multi Jet Fusion systems. Their working envelope of 380 x 284 x 380 mm can produce up to 80,000 cm3 per hour – not far off some injection molding setups.
And Carbon’s huge 190x315x330 mm build volume can create 500,000+ parts per year using their ultrafast DLS process.
So while injection molding wins on scale for now, some 3d printing systems are catching up.
Cycle Time
Cycle time measures how long it takes to create each part. And injection molding ratios are hard to beat.
For simple parts, injection molding can spit out 20+ parts per minute from some high-end systems.
In contrast, let’s look at Origin One by Origin:
- 165 parts per day
- 24 hour operation = 165 parts
- 60 mins per hour = 1 part per 22 minutes
So for basic components, the cycle time favor lies with injection molding. However, part complexity plays a role here too…
Design Complexity
When it comes to complex geometries, 3d printing has a clear edge.
The layer-upon-layer build process used in 3d printing means it can create almost any shape.
Injection molding requires molds – so part designs need to allow finished parts to be easily released.
Undercuts, negative features, and super-fine details just won’t work. If they do, you’ll pay big bucks for multi-part molds and cleanout processes post-molding.
By removing these restrictions, 3d printing can create items impossible to achieve otherwise.
So for cutting-edge parts leveraging complex decentralized lattices and intricate hollow forms, 3d printing wins out.
Part Cost
Now arguably the most important factor – how much does each part cost to manufacture?
Due to the high tooling costs, injection molding only becomes economical at higher volumes – usually 10,000+. For short runs, the costs are prohibitively high.
3d printing, however, has a much lower breakeven point. In fact, it can offer more cost efficiency for batches of 50-5,000 parts.
Let’s say you need 500 small widgets per year.
- Injection molding – Machining the mold would cost upwards of $10-20k. Then you need to buy an injection molding machine (tens of thousands of dollars) and source plastic pellets.
- 3D printing – No tooling costs. Just design the part and send it to a production 3d printing bureau like Protolabs.
Even if the per-unit 3d printing cost is higher, the total Outlay will likely favor 3d printing for these mid-sized batches.
And with advanced additive techniques like CLIP lowering raw material costs, the crossover point where 3d printing wins gets even smaller.
Surface Finish
Injection molding, even without polishing the molds, can achieve extremely smooth surface finishes down to 0.5 Ra and below.
The fused layering process of 3d printing intrinsically leads to visible stepping lines on sloping surfaces. The smallest commercial layer height of around 0.025 mm leaves a gritty texture.
So parts relying on super-fine surface finish – like lenses or reflective optics – can’t currently leverage 3d printing.
That said, techniques like chemical smoothing applied after the build process can reduce layer visibility significantly.
Accuracy & Tolerances
Again, injection molding holds an advantage over most 3d printing when tolerances under 50 microns are needed.
Machined metal molds can reliably output parts within ±0.005 mm (±0.0002″). Plus the repeatability from one component to the next beats additive manufacturing.
However, some 3d printing methods can achieve fine details too. For example, CLIP boasts accuracy to within ~10 μm, while binder jetting (~15 μm) also impresses.
So while injection molding broadly exceeds 3d printing for ultra-high precision needs, certain additive processes can match simpler injection molding accuracy.
Material Choice
With over 30,000 grades available, injection molding offers the widest material selection. Standard resins span PP, PE, POM, PC and beyond, often modified with custom additives.
3d printing polymers currently number closer to 100. But new formulations emerge regularly – high-temp PEEK and PEKK show additive manufacturing’s potential.
The range spans flexible TPU filament for FDM through to somos resin for sterolithography and CLIP optimized liquid polymers. Material choice expands yearly.
Further extending capabilities, composites like continuous carbon fiber blended with PEKK and PEEK bolster mechanical performance.
So broadly, injection molding provides the widest material selection. But with advanced additive polymers and composites closing the gap, 3d printing could catch up before long.
Will 3D Printing Completely Usurp Injection Molding?
In the near future, I don’t see 3d printing overthrowing injection molding completely. Here’s why:
Billions of Parts
For ultra-high volume applications (think billions of parts per year), additive manufacturing doesn’t yet compete.
Leading systems from Carbon and HP print hundreds of thousands of components annually at best.
However factories in China output multiple millions of parts daily across tens of thousands of injection molding machines.
So despite advances, huge-scale injection molding for mass-market parts remains unmatched.
Niche Applications
Certain applications rely on properties only currently possible through injection molding.
For example, from John’s viewpoint, medical components leveraging specialized resins are tricky to re-create through 3d printing.
And optical lenses reaching Abbe Values only possible with injection molded acrylics and polycarbonates cannot transition to additive manufacturing yet.
So specialized injection molding undoubtedly still serves critical niches that developing 3d printing has yet to replicate.
Ubiquitous Supply Chain
Injection molding boasts a vast, entrenched ecosystem. From press capacity through to trusted materials supply chains and secondary processing.
Additive manufacturing cannot yet access the scale of infrastructure. Supply bottlenecks around printers, resins, finishing and part inspection restrict the rate of expansion.
Now that’s not to say the supply chain ecosystem isn’t evolving fast. But it’s still decades behind injection molding networks built up over almost 100 years.
So until the distribution channels for polymer materials and system production throughput expand exponentially, injection molding retains supply chain dominance.
The Verdict: Coexistence Not Displacement
After comparing key metrics around scale, cost, speed, quality and capabilities, the conclusion is clear.
In 2024 and the immediate future, 3d printing absolutely does not replace injection molding entirely.
The two manufacturing platforms complement each other.
John summarizes it best:
“3d printing permits new designs impossible with injection molding. And additive techniques offer greater flexibility in production volumes.”
“But for mass-manufacturing billions of high-quality parts, leveraging established materials and supply chains – injection molding still reigns.”
So rather than framing additive technologies as usurping traditional techniques, it’s better to recognize the strengths each provides.
With that perspective, both 3d printing and injection molding manufacturing continue advancing industry into the future.
Just imagine the innovations possible when applying each technology where it works best!
The Future Of Manufacturing
I firmly believe additive manufacturing and injection molding both have bright futures.
As John suggested, hybrid modeling combining both techniques is where things get really interesting.
Expect astounding new applications of:
- 3d printed injection molds – enabling complex conformal cooling channels impossible with CNC machining
- Injection molded 3d printing resins – bringing higher precision and innovative polymers to additive manufacturing
- 3d printed injection molding release agents – revolutionizing nano-structured surfaces to slash mold release forces
- 3d printing secondary processes – enabling mass-finishing like pad printing of injection molded parts on customer-specific bases
And these crossover techniques are just the start…
The synergy possible when blending aspects of injection molding and 3d printing perhaps poses the most exciting innovations our industry will see for years to come.
So forget trying to predict if 3d printing will replace injection molding outright.
The future is all about integration, not displacement.
Combining both technologies is where we’ll discover the next manufacturing revolution.
Will 3d Printing Replace Injection Molding?
To conclude – 3d printing is making great strides towards competing with injection molding across many fronts.
For short run production, highly complex parts, and bridge manufacturing scenarios, 3d printing likely already supersedes injection molding capabilities today. However for mass-manufacturing billions of low-cost, highly accurate parts, injection molding retains dominance (for now!).
Rather than a face off between the two methods, I foresee hybrid strategies where 3d printing and injection molding complement one another for years to come.
So no – based on current trends, 3d printing certainly won’t wholly replace injection molding in the foreseeable future. But with development trajectories as they stand, anything is possible long-term…