Injection molding is one of the most popular manufacturing processes for mass production of plastic parts. However, one common challenge is producing parts that end up heavier than intended, increasing material costs and impacting functionality. So how can we reduce part weight in injection molding?
In this comprehensive guide, as a professional plastic injection molding manufacturer, we’ll dig into the root causes of excessive part weight and actionable strategies to optimize for lightweighting in injection molding. Whether you’re a mold designer, process engineer, or work on the manufacturing floor, you’ll discover tons of tips to slash grams and take costs out of plastic parts.
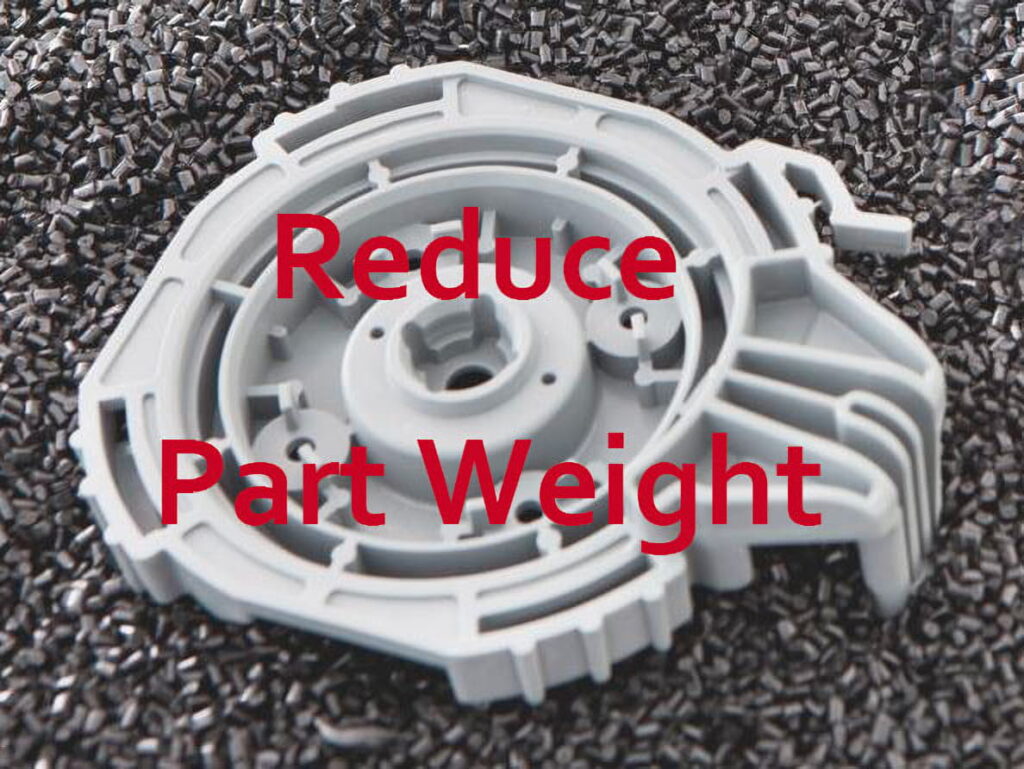
Why Part Weight Matters in Injection Molding
Let’s kick things off by reviewing why part weight is so crucial in injection molded components and end-use applications:
Reduced Raw Material Costs
Heavier parts consume more plastic resin per piece, directly raising your material costs. By optimizing lightweighting, you slash plastic usage leading to significant cost savings – especially for large production volumes.
Improved Mechanical Performance
Lower mass results in better strength-to-weight ratios, acceleration, fluid dynamic properties, and lower inertia in motion systems. This leads to better performing end-products for the same plastic resin.
Faster Cycle Times
Excess plastic increases solidification times, as the molten polymer takes longer to thoroughly cool within thicker sections. Lower mass parts cool faster, allowing faster cycle times and higher manufacturing throughput.
Enables Miniaturization
Weight savings frees up design space enabling further compaction and geometry restrictions for ever-shrinking electronics, handheld devices, and components.
Greater Sustainability
Optimizing part weight ultimately leads to sizable reductions in overall plastic consumption resulting in improved sustainability metrics from raw material savings.
Root Causes of Heavy Parts in Injection Molding
Before we dive into the solutions, it’s import to call out the three major root causes of overweight injection molded components:
1. Overpacking
Overpacking occurs when too much molten plastic is injected into the mold cavity, above what is required to completely fill the part geometry. This additional polymer leads to thicker, heavier parts.
Causes of overpacking include excessive injection pressure, slow injection speeds, low mold temperatures, and inadequate ventilation for air and gases to escape the cavity.
2. Excess Wall Thickness
Another obvious source of chunky parts is designing sections thicker than what’s required for the target mechanical performance. Thicker walls add safety factors to account for polymer behavior unknowns and manufacturing variability.
3. Poor Cooling Efficiency
Inefficient cooling leads to greater molded-in stresses producing excessive post-mold shrinkage and warpage. To compensate, molds will pack in more material to hit target dimensions resulting in overweight parts once they cool down.
How to Reduce Part Weight in Injection Molding?
Below are my top 11 methods to help injection mold lightweight parts with the same or better mechanical performance.
1. Tweak Injection Pressure Ramp
Tune injection pressure profiles to completely fill – but not overpack – mold cavities. Work with your machine technicians to optimize injection velocity and switchover points to manage precise material deposition.
Be sure to account for material viscosity changes from colorants, fillers, and regrind levels which impact flow properties.
2. Increase Injection Speed
Faster injection velocities result in improved cavity filling, especially for long, thin-wall components. Maintain mold pack pressures to ensure proper fusion and consolidation without overpacking the mold.
Again monitor effects from frictional heating on viscosity and cooling rate, as faster velocities will raise melt temperatures.
3. Add Venting Channels
Proper venting allows trapped gases and air to evacuate the mold during filling, preventing backpressure buildup which can lead to short shots or burn marks. This minimizes the extra cushion material packed in to compensate.
Venting channels require longer cycle times to have useful impact, so balance throughput goals.
4. Design Ribbed & Corrugated Features
Ribs and gussets mold easily while stiffening parts at optimized mass compared to solid sections. By designing proper rib parameters between 0.5-1x wall thickness and rib height under 3x thickness, sizable weight savings are possible.
Analyze rib trade-offs between balancing strength, filling behavior, and ejection requirements for your specific resin and geometry.
5. Specify High-Fluidity Engineering Resins
Specifying lower viscosity materials like polysulfones (PSU), polyetherimide (PEI), and liquid crystal polymers (LCP) enhance melt flow for challenging thin or long wall designs. This minimizes wall thickness requirements to hit mechanical targets.
6. Optimize Cooling Layout
Reconfigure cooling circuits to boost efficiency which minimizes molded-in stress and post-mold shrinkage that can lead to extra material deposition. Evaluate faster-cycling resins if heat removal rates become limiting.
7. Lower Melt & Mold Temperatures
Reduce barrel and mold temperatures (independently) to manage filling and reduce cycle times. Too high levels lead to lower melt viscosity and incomplete fusion requiring extra packing pressure.
Balance potential loss of dimensional stability and replication fidelity from low mold temps which can drive greater shrinkage.
8. Downgauge Wall Thicknesses
Rightsize wall thicknesses to application requirements – neither too thick nor too thin. Thickness simulation software can help rapidly iterate configurations to cut weight for functionality.
Remember to match surface quality and cosmetic goals in visible areas and compensate for thinner areas with texturing.
9. Utilize Gas-Assist Injection Molding
Inject pressurized nitrogen or carbon dioxide into the mold cavity to form hollow channels within parts after initial material deposition. The resultant foam structure allows weight savings through lower density cores.
10. Adopt Microcellular Foaming Processes
Microcellular technology like Trexel’s MuCell® solution uses gas to create tiny bubbles in the polymer during filling to reduce density up to 15%. This unique lightweighting approach causes no loss in mechanical properties.
The process requires modified tooling and machines for foaming agent metering so upfront cost is higher.
11. Embrace Metal-to-Plastic Conversions
As material performance continuously improves in rigidity, heat resistance, and other metrics – injection molded thermoplastics or thermoset composites can replace higher density metals. This drop-in substitution leads to lighter end-use articles.
Carefully evaluate design, tooling, process implications when attempting conversions without compromising product functionality. Factor in economic trade-offs over entire application lifecycles.
Take Away: Lightweighting Demands a Holistic Approach
As you’ve learned here, optimizing injection molded part weight requires careful assessment across the entire product development and production chain.
Tweaking an individual lever in isolation often fails from unanticipated changes or knock-on effects to other parameters. Plus, lightweighting inherently involves balancing trade-offs between performance, manufacturability, and economics.
Instead, a systematic methodology considering design principles, advanced resins, process refinements, tooling innovations, and even shifts to alternate manufacturing becomes necessary.
Manufacturers who can flexibly navigate these options while understanding part requirements and their manufacturing ecosystem will stand the best chance of realizing lightweight potential.
So start evaluating your own process with a spirit of experimentation – methodically assessing impacts of individual variables through DOEs (designed experiments) and process simulators. Opportunities for injection mold weight reduction hide around every corner!