Das Spritzgießen ist eines der beliebtesten Herstellungsverfahren für die Massenproduktion von Kunststoffteilen. Eine häufige Herausforderung ist jedoch die Herstellung von Teilen, die schwerer sind als vorgesehen, was die Materialkosten erhöht und die Funktionalität beeinträchtigt. Wie können wir also das Gewicht der Teile beim Spritzgießen reduzieren?
In diesem umfassenden Leitfaden finden Sie als Fachmann Hersteller von Kunststoff-Spritzgussteilengehen wir den Ursachen für übermäßiges Teilegewicht auf den Grund und zeigen Strategien zur Optimierung der Leichtbauweise beim Spritzgießen auf. Ganz gleich, ob Sie Werkzeugkonstrukteur, Verfahrenstechniker oder in der Fertigung tätig sind, Sie werden jede Menge Tipps zur Gewichtsreduzierung und Kostenreduzierung bei Kunststoffteilen entdecken.
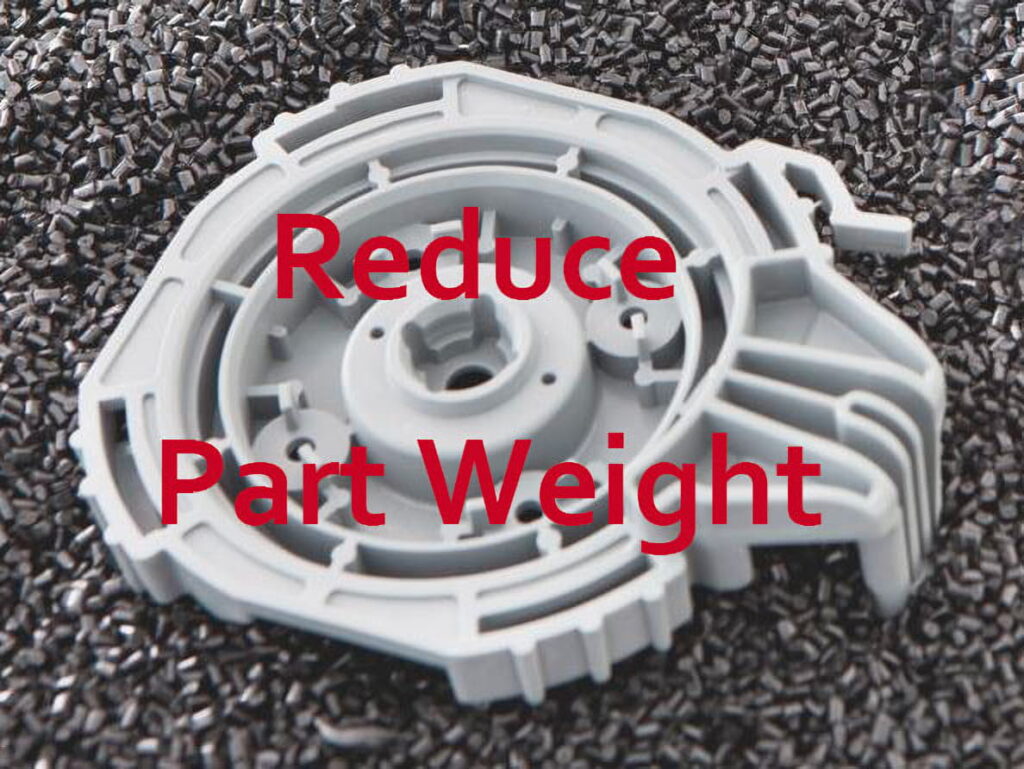
Warum das Teilegewicht beim Spritzgießen wichtig ist
Beginnen wir damit, dass wir uns ansehen, warum das Teilegewicht bei spritzgegossenen Komponenten und Endanwendungen so wichtig ist:
Reduzierte Rohstoffkosten
Schwerere Teile verbrauchen mehr Kunststoff pro Stück, was Ihre Materialkosten direkt erhöht. Durch die Optimierung des Leichtbaus können Sie den Kunststoffverbrauch senken, was zu erheblichen Kosteneinsparungen führt - insbesondere bei großen Produktionsmengen.
Verbesserte mechanische Leistung
Eine geringere Masse führt zu einem besseren Verhältnis von Festigkeit zu Gewicht, Beschleunigung, fluiddynamischen Eigenschaften und geringerer Trägheit in Bewegungssystemen. Dies führt zu leistungsfähigeren Endprodukten für denselben Kunststoff.
Schnellere Zykluszeiten
Überschüssiger Kunststoff verlängert die Erstarrungszeiten, da das geschmolzene Polymer in dickeren Abschnitten länger braucht, um vollständig abzukühlen. Teile mit geringerer Masse kühlen schneller ab, was kürzere Zykluszeiten und einen höheren Fertigungsdurchsatz ermöglicht.
Ermöglicht Miniaturisierung
Durch die Gewichtseinsparungen wird Konstruktionsraum frei, der weitere Verdichtungen und Geometriebeschränkungen für immer kleiner werdende Elektronik, Handheld-Geräte und Komponenten ermöglicht.
Größere Nachhaltigkeit
Die Optimierung des Teilegewichts führt letztlich zu einer beträchtlichen Verringerung des Gesamtkunststoffverbrauchs und damit zu einer Verbesserung der Nachhaltigkeitskennzahlen durch Einsparungen bei den Rohstoffen.
Ursachen für schwere Teile beim Spritzgießen
Bevor wir uns mit den Lösungen befassen, ist es wichtig, die drei Hauptursachen für übergewichtige Spritzgussteile zu nennen:
1. Umverpacken
Eine Überfüllung tritt auf, wenn zu viel geschmolzener Kunststoff in den Formhohlraum eingespritzt wird, als für die vollständige Ausfüllung der Teilegeometrie erforderlich ist. Dieses zusätzliche Polymer führt zu dickeren, schwereren Teilen.
Zu den Ursachen für Überfüllungen gehören ein zu hoher Einspritzdruck, langsame Einspritzgeschwindigkeiten, niedrige Werkzeugtemperaturen und eine unzureichende Entlüftung, damit Luft und Gase aus der Kavität entweichen können.
2. Überschüssige Wanddicke
Eine weitere offensichtliche Ursache für klobige Teile ist die Konstruktion von Abschnitten, die dicker sind als für die angestrebte mechanische Leistung erforderlich. Bei dickeren Wänden werden Sicherheitsfaktoren hinzugefügt, um das unbekannte Polymerverhalten und die Fertigungsvariabilität zu berücksichtigen.
3. Schlechte Kühleffizienz
Eine ineffiziente Abkühlung führt zu größeren Spannungen in der Form und damit zu übermäßigem Schwund und Verzug nach dem Guss. Um dies zu kompensieren, packen die Formen mehr Material ein, um die Zielmaße zu erreichen, was zu übergewichtigen Teilen führt, sobald sie abgekühlt sind.
Wie lässt sich das Teilegewicht beim Spritzgießen reduzieren?
Im Folgenden finden Sie meine 11 besten Methoden, um leichte Teile bei gleicher oder besserer mechanischer Leistung zu spritzen.
1. Tweak Einspritzdruckrampe
Stimmen Sie die Einspritzdruckprofile so ab, dass die Kavitäten vollständig gefüllt, aber nicht überfüllt werden. Arbeiten Sie mit Ihren Maschinentechnikern zusammen, um die Einspritzgeschwindigkeit und die Umschaltpunkte zu optimieren und eine präzise Materialabscheidung zu erreichen.
Berücksichtigen Sie unbedingt die Viskositätsänderungen des Materials durch Farbstoffe, Füllstoffe und Mahlgut, die die Fließeigenschaften beeinflussen.
2. Einspritzgeschwindigkeit erhöhen
Schnellere Einspritzgeschwindigkeiten führen zu einer besseren Füllung der Kavitäten, insbesondere bei langen, dünnwandigen Komponenten. Aufrechterhaltung des Packungsdrucks, um eine ordnungsgemäße Verschmelzung und Konsolidierung zu gewährleisten, ohne die Form zu überfüllen.
Überwachen Sie auch hier die Auswirkungen der Reibungserwärmung auf die Viskosität und die Abkühlungsgeschwindigkeit, da schnellere Geschwindigkeiten die Schmelztemperaturen erhöhen.
3. Belüftungskanäle hinzufügen
Durch eine ordnungsgemäße Entlüftung können eingeschlossene Gase und Luft während des Füllens aus der Form entweichen, wodurch der Aufbau eines Gegendrucks verhindert wird, der zu kurzen Schüssen oder Brandflecken führen kann. Dadurch wird das zusätzliche Polstermaterial, das zum Ausgleich eingepackt wird, minimiert.
Entlüftungskanäle benötigen längere Zykluszeiten, um eine sinnvolle Wirkung zu erzielen, daher sollten die Durchsatzziele abgewogen werden.
4. Design gerippt & gewellt Merkmale
Rippen und Zwickel lassen sich leicht formen und versteifen die Teile bei optimierter Masse im Vergleich zu Vollprofilen. Durch die Gestaltung geeigneter Rippenparameter zwischen 0,5-1x Wanddicke und einer Rippenhöhe unter 3x Dicke sind beträchtliche Gewichtseinsparungen möglich.
Analysieren Sie Rippenkompromisse zwischen Festigkeit, Füllverhalten und Ausstoßanforderungen für Ihren spezifischen Kunststoff und Ihre Geometrie.
5. Spezifizieren Sie hochfließfähige technische Harze
Die Verwendung von Materialien mit niedrigerer Viskosität wie Polysulfone (PSU), Polyetherimid (PEI) und Flüssigkristallpolymere (LCP) verbessern den Schmelzfluss bei anspruchsvollen dünnen oder langwandigen Konstruktionen. Dies minimiert die Anforderungen an die Wandstärke, um die mechanischen Ziele zu erreichen.
6. Optimierung der Kühlungsanordnung
Rekonfigurieren Sie die Kühlkreisläufe, um die Effizienz zu steigern, und minimieren Sie so die Spannungen in der Form und die Schrumpfung nach der Form, die zu einer zusätzlichen Materialablagerung führen kann. Evaluieren Sie schneller zyklierende Harze, wenn die Wärmeabfuhrraten zu einem Hindernis werden.
7. Niedrigere Schmelz- und Formtemperaturen
Senken Sie die Zylinder- und Werkzeugtemperaturen (unabhängig voneinander), um die Befüllung zu steuern und die Zykluszeiten zu verkürzen. Zu hohe Werte führen zu einer geringeren Viskosität der Schmelze und einer unvollständigen Verschmelzung, die einen zusätzlichen Verpackungsdruck erfordert.
Ausgleich des potenziellen Verlusts an Dimensionsstabilität und Replikationstreue durch niedrige Formtemperaturen, die zu größerer Schrumpfung führen können.
8. Wandstärken nach unten messen
Passen Sie die Wandstärken an die Anwendungsanforderungen an - weder zu dick noch zu dünn. Software zur Dickensimulation kann dabei helfen, Konfigurationen schnell zu iterieren, um Gewicht für Funktionalität zu sparen.
Denken Sie daran, die Oberflächenqualität und die kosmetischen Ziele in den sichtbaren Bereichen abzustimmen und dünnere Bereiche durch Texturierung auszugleichen.
9. Gasunterstütztes Spritzgießen verwenden
Injektion von Stickstoff oder Kohlendioxid unter Druck in den Formhohlraum zur Bildung von Hohlkanälen in den Teilen nach der ersten Materialabscheidung. Die resultierende Schaumstruktur ermöglicht Gewichtseinsparungen durch Kerne mit geringerer Dichte.
10. Einführung von mikrozellularen Schäumungsprozessen
Die mikrozellulare Technologie wie die MuCell®-Lösung von Trexel nutzt Gas, um während des Füllens winzige Bläschen im Polymer zu erzeugen und so die Dichte auf bis zu 15% zu reduzieren. Dieser einzigartige Ansatz zur Gewichtsreduzierung verursacht keinen Verlust an mechanischen Eigenschaften.
Das Verfahren erfordert modifizierte Werkzeuge und Maschinen für die Schaummitteldosierung, so dass die Anschaffungskosten höher sind.
11. Metall-Kunststoff-Umwandlungen begrüßen
Da sich die Leistungsfähigkeit von Werkstoffen in Bezug auf Steifigkeit, Hitzebeständigkeit und andere Kriterien kontinuierlich verbessert, können spritzgegossene Thermoplaste oder duroplastische Verbundwerkstoffe Metalle mit höherer Dichte ersetzen. Diese Drop-in-Substitution führt zu leichteren Endverbrauchsartikeln.
Bewerten Sie sorgfältig die Auswirkungen auf Design, Werkzeuge und Prozesse, wenn Sie versuchen, Umstellungen vorzunehmen, ohne die Produktfunktionalität zu beeinträchtigen. Berücksichtigen Sie wirtschaftliche Kompromisse über den gesamten Lebenszyklus der Anwendung.
Mitnehmen: Lightweighting erfordert einen ganzheitlichen Ansatz
Wie Sie hier erfahren haben, erfordert die Optimierung des Gewichts von Spritzgussteilen eine sorgfältige Bewertung über die gesamte Produktentwicklungs- und Produktionskette hinweg.
Die Optimierung eines einzelnen Hebels scheitert oft an unvorhergesehenen Änderungen oder Auswirkungen auf andere Parameter. Außerdem müssen beim Leichtbau naturgemäß Kompromisse zwischen Leistung, Herstellbarkeit und Wirtschaftlichkeit eingegangen werden.
Stattdessen ist eine systematische Methodik erforderlich, die Konstruktionsprinzipien, fortschrittliche Kunststoffe, Prozessverfeinerungen, Werkzeuginnovationen und sogar die Umstellung auf eine alternative Fertigung berücksichtigt.
Hersteller, die in der Lage sind, diese Optionen flexibel zu nutzen und gleichzeitig die Anforderungen an die Teile und ihr Produktionssystem zu verstehen, haben die besten Chancen, das Leichtbaupotenzial auszuschöpfen.
Beginnen Sie also damit, Ihren eigenen Prozess mit Experimentiergeist zu evaluieren, indem Sie die Auswirkungen der einzelnen Variablen methodisch durch DOEs bewerten (geplante Experimente) und Prozesssimulatoren. Möglichkeiten zur Gewichtsreduzierung von Spritzgießwerkzeugen verbergen sich hinter jeder Ecke!