Formowanie wtryskowe jest jednym z najpopularniejszych procesów produkcji masowej części z tworzyw sztucznych. Jednak jednym z powszechnych wyzwań jest produkcja części, które są cięższe niż zamierzano, co zwiększa koszty materiałów i wpływa na funkcjonalność. Jak więc możemy zmniejszyć wagę części w formowaniu wtryskowym?
W tym kompleksowym przewodniku, jako profesjonalista Producent form wtryskowych z tworzyw sztucznychW tym artykule omówimy podstawowe przyczyny nadmiernej masy części i praktyczne strategie optymalizacji pod kątem lekkości w formowaniu wtryskowym. Niezależnie od tego, czy jesteś projektantem form, inżynierem procesu, czy pracujesz na hali produkcyjnej, odkryjesz mnóstwo wskazówek, jak zmniejszyć gramaturę i obniżyć koszty części z tworzyw sztucznych.
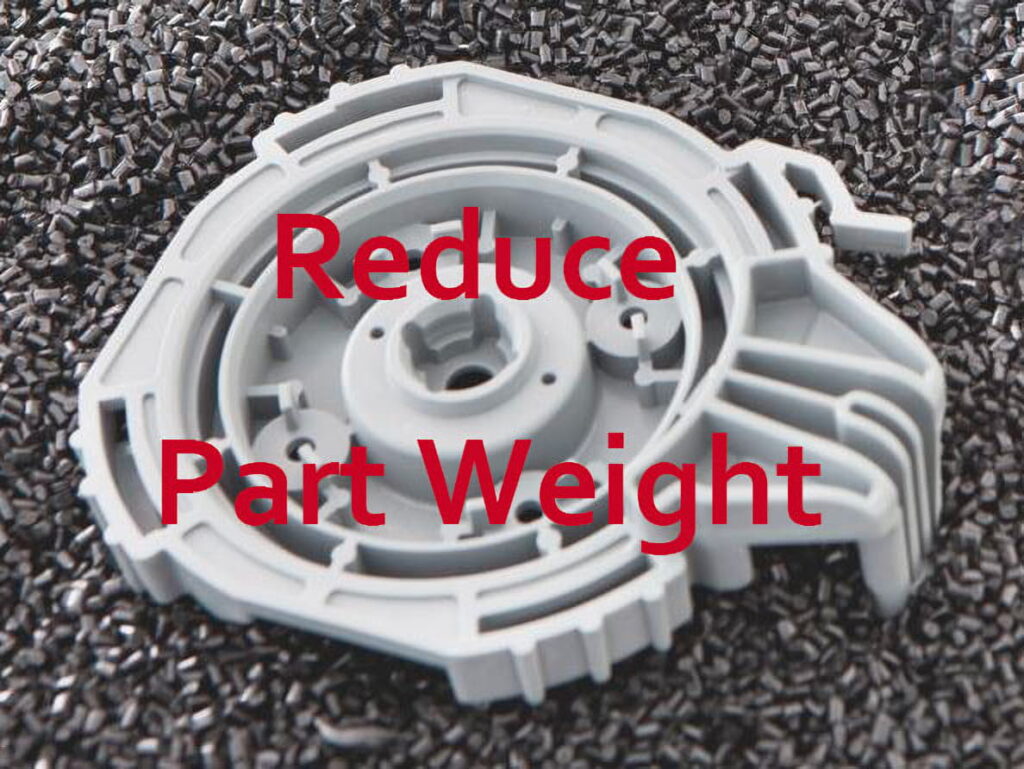
Dlaczego masa części ma znaczenie w formowaniu wtryskowym
Zacznijmy od sprawdzenia, dlaczego masa części jest tak ważna w przypadku elementów formowanych wtryskowo i zastosowań końcowych:
Niższe koszty surowców
Cięższe części zużywają więcej żywicy plastikowej na sztukę, co bezpośrednio zwiększa koszty materiałów. Optymalizacja lekkości pozwala zmniejszyć zużycie tworzyw sztucznych, co prowadzi do znacznych oszczędności kosztów - zwłaszcza w przypadku dużych wolumenów produkcji.
Ulepszona wydajność mechaniczna
Niższa masa skutkuje lepszym stosunkiem wytrzymałości do masy, przyspieszeniem, właściwościami dynamicznymi płynów i mniejszą bezwładnością w systemach ruchu. Prowadzi to do lepszej wydajności produktów końcowych dla tej samej żywicy z tworzywa sztucznego.
Krótsze czasy cyklu
Nadmiar tworzywa sztucznego wydłuża czas krzepnięcia, ponieważ dokładne schłodzenie stopionego polimeru w grubszych sekcjach trwa dłużej. Części o mniejszej masie stygną szybciej, co pozwala na skrócenie czasu cyklu i zwiększenie wydajności produkcji.
Umożliwia miniaturyzację
Oszczędność wagi uwalnia przestrzeń projektową, umożliwiając dalsze zagęszczanie i ograniczenia geometrii dla stale kurczącej się elektroniki, urządzeń przenośnych i komponentów.
Większy zrównoważony rozwój
Optymalizacja wagi części ostatecznie prowadzi do znacznego zmniejszenia ogólnego zużycia tworzyw sztucznych, co skutkuje poprawą wskaźników zrównoważonego rozwoju dzięki oszczędności surowców.
Przyczyny powstawania ciężkich części w procesie formowania wtryskowego
Zanim zagłębimy się w rozwiązania, ważne jest, aby wymienić trzy główne przyczyny nadwagi komponentów formowanych wtryskowo:
1. Przepakowywanie
Nadmierne upakowanie występuje, gdy do gniazda formy wtryskiwana jest zbyt duża ilość stopionego tworzywa sztucznego, przekraczająca ilość wymaganą do całkowitego wypełnienia geometrii części. Ten dodatkowy polimer prowadzi do powstania grubszych i cięższych części.
Przyczyny nadmiernego pakowania obejmują nadmierne ciśnienie wtrysku, niskie prędkości wtrysku, niskie temperatury formy i nieodpowiednią wentylację, aby powietrze i gazy mogły wydostać się z wnęki.
2. Nadmierna grubość ścianki
Innym oczywistym źródłem grubych części jest projektowanie sekcji grubszych niż jest to wymagane dla docelowej wydajności mechanicznej. Grubsze ścianki dodają współczynniki bezpieczeństwa w celu uwzględnienia niewiadomych dotyczących zachowania polimeru i zmienności produkcji.
3. Niska wydajność chłodzenia
Nieefektywne chłodzenie prowadzi do większych naprężeń w formie, powodując nadmierny skurcz i wypaczenie po formowaniu. Aby to zrekompensować, formy będą pakować więcej materiału, aby osiągnąć docelowe wymiary, co skutkuje nadwagą części po ostygnięciu.
Jak zmniejszyć wagę części w formowaniu wtryskowym?
Poniżej przedstawiam 11 najlepszych metod pomagających w formowaniu wtryskowym lekkich części o takich samych lub lepszych parametrach mechanicznych.
1. Rampa ciśnienia wtrysku
Dostosuj profile ciśnienia wtrysku, aby całkowicie wypełnić - ale nie przepełnić - gniazda formy. Współpracuj z technikami maszyn, aby zoptymalizować prędkość wtrysku i punkty przełączania w celu precyzyjnego osadzania materiału.
Należy pamiętać o uwzględnieniu zmian lepkości materiału spowodowanych barwnikami, wypełniaczami i poziomami przemiału, które wpływają na właściwości płynięcia.
2. Zwiększenie prędkości wtrysku
Większa prędkość wtrysku skutkuje lepszym wypełnieniem gniazda, szczególnie w przypadku długich, cienkościennych elementów. Utrzymuj ciśnienie w formie, aby zapewnić prawidłową fuzję i konsolidację bez przepełniania formy.
Ponownie należy monitorować wpływ ogrzewania tarciowego na lepkość i szybkość chłodzenia, ponieważ większe prędkości spowodują wzrost temperatury stopu.
3. Dodaj kanały wentylacyjne
Odpowiednie odpowietrzenie pozwala uwięzionym gazom i powietrzu opróżnić formę podczas napełniania, zapobiegając tworzeniu się przeciwciśnienia, które może prowadzić do krótkich strzałów lub śladów wypalenia. Pozwala to zminimalizować ilość dodatkowego materiału wypełniającego.
Kanały odpowietrzające wymagają dłuższych czasów cyklu, aby mieć użyteczny wpływ, więc należy zrównoważyć cele przepustowości.
4. Konstrukcja żebrowana i falista
Żebra i kliny łatwo się formują, jednocześnie usztywniając części przy zoptymalizowanej masie w porównaniu z sekcjami pełnymi. Projektując odpowiednie parametry żeber w zakresie 0,5-1x grubość ścianki i wysokość żeber poniżej 3x grubość, można uzyskać znaczne oszczędności masy.
Przeanalizuj kompromisy między wytrzymałością żeber, zachowaniem wypełnienia i wymaganiami dotyczącymi wyrzutu dla konkretnej żywicy i geometrii.
5. Określ żywice inżynieryjne o wysokiej płynności
Materiały o niższej lepkości, takie jak polisulfony (PSU), polieteroimid (PEI) i polimery ciekłokrystaliczne (LCP), poprawiają przepływ stopu w przypadku trudnych projektów cienkich lub długich ścianek. Minimalizuje to wymagania dotyczące grubości ścianek, aby osiągnąć cele mechaniczne.
6. Optymalizacja układu chłodzenia
Rekonfiguracja obwodów chłodzenia w celu zwiększenia wydajności, co minimalizuje naprężenia w formie i skurcz po formowaniu, które mogą prowadzić do dodatkowego osadzania się materiału. Ocena żywic o szybszym cyklu, jeśli szybkość usuwania ciepła staje się ograniczająca.
7. Niższe temperatury topienia i formowania
Zmniejsz temperaturę beczki i formy (niezależnie), aby zarządzać napełnianiem i skrócić czas cyklu. Zbyt wysokie poziomy prowadzą do niższej lepkości stopu i niepełnego stopienia wymagającego dodatkowego ciśnienia pakowania.
Równowaga potencjalnej utraty stabilności wymiarowej i wierności replikacji z powodu niskich temperatur formy, które mogą powodować większy skurcz.
8. Grubość ścianki w dół
Dopasuj grubość ścianki do wymagań aplikacji - ani za gruba, ani za cienka. Oprogramowanie do symulacji grubości może pomóc w szybkiej iteracji konfiguracji w celu zmniejszenia masy i zwiększenia funkcjonalności.
Pamiętaj, aby dopasować jakość powierzchni i cele kosmetyczne w widocznych obszarach i zrekompensować cieńsze obszary teksturowaniem.
9. Wykorzystanie formowania wtryskowego ze wspomaganiem gazowym
Wtryskiwanie azotu lub dwutlenku węgla pod ciśnieniem do gniazda formy w celu utworzenia pustych kanałów w częściach po wstępnym osadzeniu materiału. Uzyskana w ten sposób struktura pianki pozwala na zmniejszenie wagi dzięki rdzeniom o niższej gęstości.
10. Przyjęcie mikrokomórkowych procesów spieniania
Technologia mikrokomórkowa, taka jak rozwiązanie MuCell® firmy Trexel, wykorzystuje gaz do tworzenia małych pęcherzyków w polimerze podczas napełniania, aby zmniejszyć gęstość do 15%. To unikalne podejście do zmniejszenia masy nie powoduje utraty właściwości mechanicznych.
Proces ten wymaga zmodyfikowanego oprzyrządowania i maszyn do dozowania środka spieniającego, więc koszty początkowe są wyższe.
11. Konwersja metalu na tworzywo sztuczne
Ponieważ wydajność materiałów stale się poprawia pod względem sztywności, odporności na ciepło i innych wskaźników - formowane wtryskowo tworzywa termoplastyczne lub kompozyty termoutwardzalne mogą zastąpić metale o większej gęstości. Ta substytucja prowadzi do lżejszych artykułów końcowych.
Staranna ocena projektu, oprzyrządowania i implikacji procesowych podczas próby konwersji bez uszczerbku dla funkcjonalności produktu. Uwzględnienie kompromisów ekonomicznych w całym cyklu życia aplikacji.
Take Away: Lekkość wymaga holistycznego podejścia
Jak dowiedziałeś się tutaj, optymalizacja masy części formowanych wtryskowo wymaga starannej oceny w całym łańcuchu rozwoju i produkcji produktu.
Ulepszanie pojedynczej dźwigni w izolacji często kończy się niepowodzeniem z powodu nieprzewidzianych zmian lub efektów domina dla innych parametrów. Ponadto, lekkość z natury wiąże się z równoważeniem kompromisów między wydajnością, możliwościami produkcyjnymi i ekonomią.
Zamiast tego konieczna staje się systematyczna metodologia uwzględniająca zasady projektowania, zaawansowane żywice, udoskonalenia procesów, innowacje w zakresie narzędzi, a nawet przejście na alternatywne metody produkcji.
Producenci, którzy potrafią elastycznie poruszać się po tych opcjach, jednocześnie rozumiejąc wymagania dotyczące części i swój ekosystem produkcyjny, będą mieli największą szansę na wykorzystanie potencjału lekkości.
Zacznij więc oceniać swój własny proces w duchu eksperymentowania - metodycznie oceniając wpływ poszczególnych zmiennych za pomocą DOE (zaprojektowane eksperymenty) i symulatory procesów. Możliwości redukcji masy form wtryskowych kryją się za każdym rogiem!